Cement plant noise has the characteristics of fixed sound source points, complex sound source types, and high sound pressure levels. For example: crushers, raw material mills, coal mills, cement mills, fans, air compressors, blowers, etc. have sound pressure levels of 80-120 dB (A), which are strong noise sources.
According to the characteristics of cement plants, there are three main noise sources in cement plants:
(a) Mill noise. The ball mill is an important grinding equipment in the cement plant. The noise level of the ball mill is as high as 100~120 dB (A) during normal operation. In cement plant production, mills are mainly used for the preparation of pulverized coal, raw meal and cement. Taking the ball mill as an example, the cylinder rotates during operation, and the mechanical noise generated by the collision of steel balls, steel balls, steel balls, and materials is radiated outward from the surface of the cylinder. The sound pressure level is between 85 and 120. Around dB(A), the peak frequency is between 500~2 000 Hz. It is characterized by high noise level, wide frequency range and long propagation distance.
(b) Fan noise. The cement mill, raw material mill, kiln tail, dust collector, etc. in the cement plant all have exhaust fans. They are the main exhaust and air supply equipment in the cement plant. The noise when the fans are working is mainly caused by air friction at the inlet and outlet and fan vibration. The noise Generally around 90 dB (A), fan noise is characterized by high sound pressure level and wide frequency range.
(c) Crusher noise. The noise in the crushing workshop of the cement plant is mainly caused by the impact and friction between the limestone materials and between the limestone and the crusher during the crushing process. For jaw crushers, hammer crushers, impact crushers commonly used in cement plants, the noise level is generally between 80 and 100 dB (A).
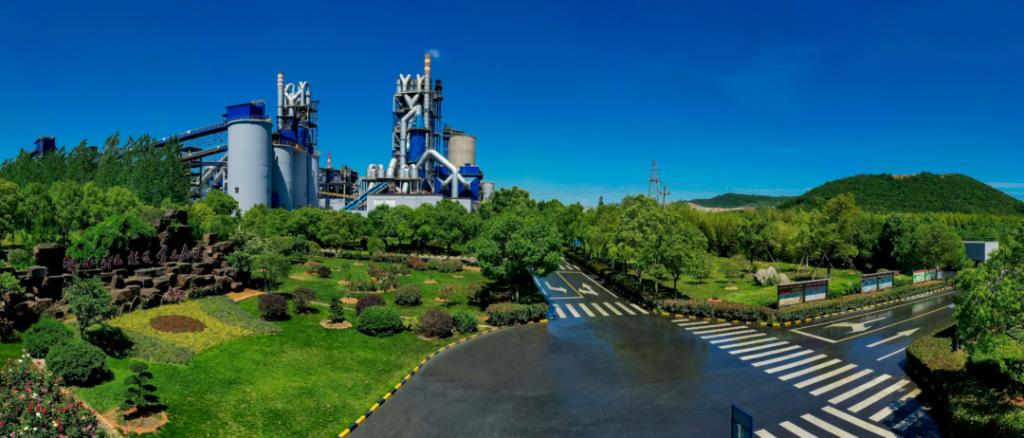
Sound source, propagation medium and receiver are the three factors that form noise pollution. The sound is first emitted due to vibration at the noise source, spreads through the air and reaches the victim. Only when these three exist at the same time will noise interference be caused to the listener. Therefore, noise control can start from three aspects: controlling the noise source, blocking the transmission path, and protecting the victim.
Control noise sources.
(a) Try to use low-noise equipment and improve the design and equipment selection plan. Before purchasing equipment, it is necessary to understand the comprehensive performance of each equipment in advance, including a detailed understanding of the intensity of the noise, and use this as an important basis for equipment selection. For example: choose a new crusher to replace the traditional crushing system; choose a vertical mill system to replace the traditional ball mill system; choose roller press grinding to replace the traditional ball mill system; choose a new screw air compressor to replace the traditional piston compression Machine; choosing low-noise fans to replace traditional fans can greatly reduce the noise level during the operation of the cement plant. For rotating mechanical equipment, adopting a low-noise transmission method can effectively reduce noise pollution. Generally, the noise generated by gear rotation devices is relatively large, so helical gears or helical gears can be used instead. If belt transmission is used instead of ordinary gear transmission, the noise can be reduced by about 16 dB (A) because the belt can act as a vibration damping resistance. ; For gear transmission devices, by reducing the linear speed of the gear and selecting an appropriate transmission ratio, the noise level can also be effectively reduced.
(b) Carry out regular inspection, maintenance and upkeep of equipment. Most cement production equipment uses electric motors as the power source to drive related power parts. Among them, the movement noise of power parts is the main noise source of the equipment. For example, when the bearings are worn and moved, harsh friction noise will be produced. Regular lubrication and maintenance of bearings, or if wear and tear is discovered and repaired in time, can effectively reduce or even eliminate this harsh friction noise.
(c) Noise control of grinding system. Selecting reasonable wear-resistant materials and steel ball gradation can improve grinding efficiency, avoid dry grinding, and reduce mill noise. Laying an elastic layer between the inner surface of the mill barrel and the lining plate eliminates the rigid connection between the two, which can reduce radiation noise. In addition, covering the outer surface of the mill barrel with a sound insulation layer (damping layer) can also reduce mill noise. The noise sources of the mill transmission mechanism are the reduction gearbox and the electric motor. When the gears in the reduction box are meshing, the friction, impact and stress changes between the teeth produce noise. Strengthening the maintenance and repair of the gears is the best way to reduce gear noise.
cement plants can be equipped with shock-absorbing pads, and if necessary, sound-absorbing materials can be installed inside the workshop to reduce noise levels. In terms of technology, the material drop should be minimized to reduce noise; in terms of production, the use of automatic control systems can also reduce noise.
(e) Fan noise control. At present, the main methods to reduce fan noise include: installing mufflers and setting up air inlet anechoic chambers. Installing mufflers at the inlet and outlet of the fan is the most effective method to reduce fan noise. However, different mufflers need to be selected for different fans. device.
(f) Vibration and noise control. In the control of noise, vibration noise is the most difficult to solve. Before purchasing equipment, the construction unit must consider the operating noise and vibration noise issues of the relevant equipment and their control measures, such as requiring the equipment manufacturer to cooperate in providing anti-vibration pads and other accessories suitable for the natural frequency of the equipment; during foundation construction and equipment installation During the inspection, phased acceptance must be carried out strictly in accordance with relevant quality control indicators, and attention must be paid to strengthening the firmness and tightness of equipment connections, which can also effectively reduce vibration and noise after the equipment is put into operation.
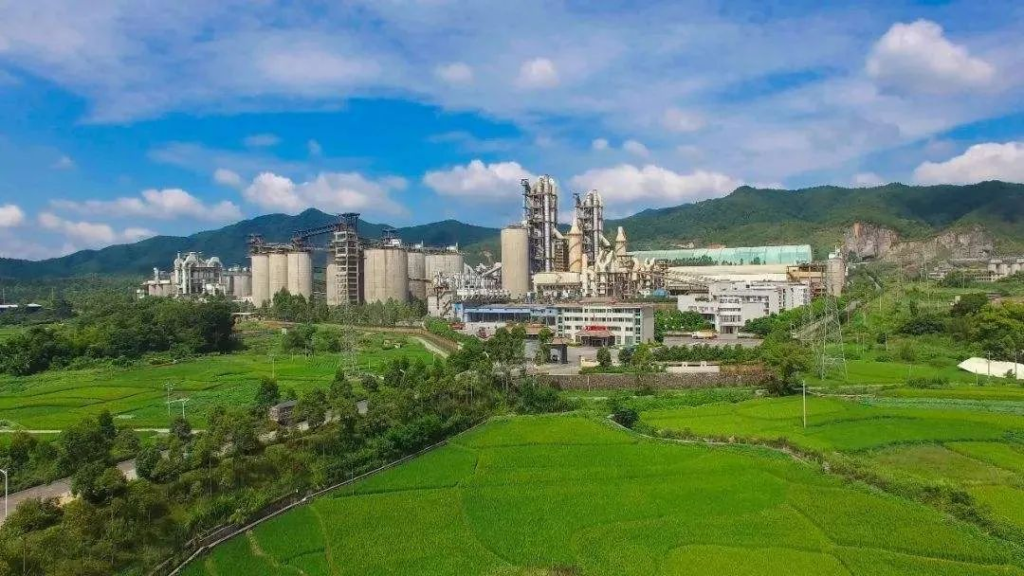
Block the transmission route.
The main methods to block the transmission path are: setting up buffer zones, that is, rationally arranging equipment with high noise; using sound absorption, sound insulation, silencing and other acoustic control technologies to cut off the noise transmission path, and equalize the noise source with the sound-sensitive residents. Protect target isolation.
(a) Set up a buffer zone and place high-noise mills, fans and other equipment away from factory employee dormitories, office areas, laboratories, residential areas and other areas to effectively reduce the impact of noise on the surrounding environment through distance attenuation.
(b) Sound absorption, insulation and silencing measures. When the source of equipment noise cannot be prevented, the impact of noise on the surrounding environment is usually reduced by sound absorption, sound insulation and sound elimination. Set up a soundproof room and seal the equipment in a small space to avoid the noise generated during its operation. This noise reduction effect is quite ideal. Mills and crushers in cement plants usually use sound-absorbing materials as walls, and soundproof rooms are
set up to control noise.
Strengthen personal protection and health monitoring
Protection solutions take a more passive approach to noise control. When measures cannot be taken on the sound source and transmission path or the results of the measures are not satisfactory, it is necessary to take protective measures for the victims, such as wearing earplugs, earmuffs or helmets for cement plant operators; for the surrounding affected residents, Soundproof doors and windows should be installed on the house; affected residents should be relocated if necessary.
In addition, for severe noise pollution from cement plants, the following measures are available:
(a) When selecting a factory site, try to avoid residential areas and other areas with higher requirements for acoustic environment, and use natural terrain such as mountains for sound insulation.
(b) Strengthen the greening of the factory area, and plant green isolation belts mainly with tall trees in the open space of the factory area and around the factory area, which will have a certain blocking effect on noise.
(c) Strengthen the management of various equipment in the factory area to ensure normal operation. Reducing the time that operators are exposed to noise can greatly reduce the harm of noise to operators. Operators can change the work system from three shifts a day to four: or rotate workers’ positions, rotating workers in high-noise workshops and low-noise workshops to reduce the time workers spend in a noisy environment and reduce noise. Impact on workers’ health.