Cement is an important basic raw material and plays an important role in social and economic construction. In 2021, world cement production will be approximately 4.28 billion tons. Cement production requires the consumption of a large amount of calcareous raw materials and fossil fuels, and the average carbon dioxide emission per unit product is about 610 kilograms. From this, it can also be deduced that the world cement industry will produce nearly 2.6 billion tons of carbon dioxide emissions in 2021, which is approximately the carbon dioxide emissions related to human production activities. 7% of the amount. Judging from the economic development status of many countries around the world, cement production still has certain growth potential, and the proportion of carbon emissions from cement production in global carbon emissions will still show an upward trend in the next few years. Carbon emission reduction is the only way for the green and sustainable development of the cement industry. It is also the opportunity and challenge faced by the cement industry.
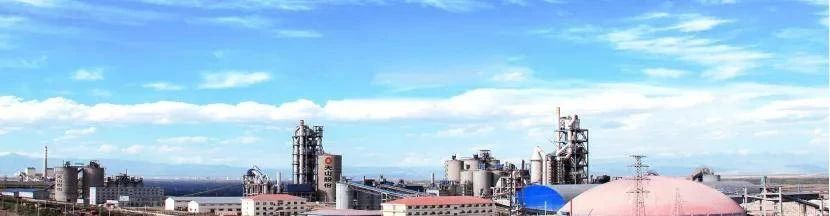
1.Current status of carbon emission reduction development in the cement industry in Asia
Most of Asia is a developing country, and cement production has continued to grow rapidly in recent decades, especially in China and India. The cement production of the two countries is about 63% of the world’s cement production.
In 2021, China’s cement output will be 2.4 billion tons and clinker output will be 1.8 billion tons, basically the same as in 2013. China is the world’s largest cement producer and consumer, accounting for about 56% of the world’s total output. However, in recent years, its output has basically stabilized at around 2.4 billion tons, indicating that its production capacity has reached its peak. Research and analysis show that China’s carbon dioxide emissions per ton of cement production are about 560 kilograms, and the carbon dioxide emissions generated by the cement industry are about 1.34 billion tons. From a technical perspective, all Chinese cement production companies have adopted new dry production technology with precalciner kilns as the core, and are equipped with low-temperature waste heat power generation and carbon reduction facilities. The overall level is at the internationally advanced level; the main energy supply fuels are coal and biomass. and waste-derived fuel account for about 2%.
In order to achieve the “double carbon” goal, the China Building Materials Federation issued the “Action Proposal to Promote Carbon Peaking and Carbon Neutrality in the Building Materials Industry”, proposing that China’s cement industry should take the lead in achieving carbon peaking before 2023, with specific carbon reduction targets. The discharge path and technical measures include: (1) Overcapacity reduction. The Chinese government implements supply-side reforms to eliminate excess production capacity. Capacity replacement is an important means to promote the supply-side reform of the cement industry, and is also an effective method to eliminate backward cement production capacity to reduce energy consumption and carbon emissions; (2) Substitute raw materials, use high calcium oxide waste residues such as carbide slag and steel slag to replace calcareous raw materials, thereby reducing Carbon dioxide emissions during the production process; (3) Alternative fuels, using biomass fuel and industrial waste to replace fossil fuels, and promoting the use of cement kiln co-processing waste technology; (4) Further improving the energy efficiency level of existing process technologies and realizing the “two aspects” of production enterprises (4) Vigorously develop and utilize new energy, make full use of wind power and photovoltaic power generation technology, and actively develop new combustion technology; (5) Research and develop carbon dioxide capture and utilization (CCUS) technology.

With the elimination of backward production capacity, China’s cement demand is close to its peak and is expected to show a gradual downward trend in the future. China’s policies guide cement companies to integrate the industrial chain, eliminate backward and redundant production capacity, and optimize the allocation of resources and technology. This will make the optimized industrial chain more efficient, and the carbon dioxide emissions per unit of cement product will gradually decrease. In terms of raw material substitution, Chinese cement companies attach greater importance to the use of high calcium oxide materials such as calcium carbide slag and steel slag as limestone substitutes to achieve carbon emission reductions in the cement production process. China’s various industrial categories are complete, and the output of high-calcium oxide industrial by-products or wastes is large. Through comprehensive utilization in cement production, multiple economic and environmental benefits can be obtained. In terms of alternative fuels, the average usage rate of material and waste-derived fuels in Chinese cement companies is low. Through policy guidance and technological innovation (such as cement kiln co-processing waste technology), alternative fuels have greater carbon reduction in the future cement production process. potential. In terms of energy efficiency technology, Chinese cement companies are more active in the research and development and application of new technologies. They are at the leading level in new dry processes and waste heat utilization. In particular, the recently implemented “two informatization” integration strategy is also conducive to production process technology. and improvement of management level. In terms of carbon dioxide capture and application, some Chinese cement companies are also actively trying to apply it, which can accumulate technology and experience for future large-scale applications.
India’s cement production in 2021 is about 300 million tons, ranking second in the world, accounting for about 7% of the world’s total cement production. The cement industry emits about 175 million tons of carbon dioxide, accounting for 8% of India’s total carbon emissions. The carbon dioxide emissions per ton of cement production are approximately 565 kilograms. India has some relatively advanced cement plants. Most of the new cement plants use precalciner kilns. The main energy supply fuels are coal accounting for 95.3%, oil accounting for 1.3%, and biomass fuel and industrial waste accounting for about 3.4%.
India’s urbanization rate is 34%, and per capita cement consumption is only 209 kg/year. In India’s cement demand structure, real estate accounts for about 67%, commercial construction accounts for 11%, infrastructure construction accounts for about 13%, and the remaining industrial construction demand accounts for 9%.
The overall carbon reduction goal of the Indian cement industry is to reduce carbon emissions to 33% to 35% of 2005 levels in 2030, to achieve a fuel substitution rate of 30%, to achieve 100% of renewable energy power generation, and to produce direct carbon dioxide per ton of cement in 2050. Emissions are reduced to 350 kilograms, and carbon neutrality is basically achieved through the application of CCUS technology.
In 2013, the Indian cement industry studied and formulated a low-carbon development roadmap, which was updated in 2018. The main technical measures include: (1) using energy-saving measures and equipment to further improve thermal energy efficiency and electricity efficiency; (2) establishing and Adopt an efficient waste heat recovery system; (3) vigorously adopt alternative raw and fuel technologies; (4) reduce the cement clinker coefficient and promote the application of mixed cement and low-carbon cement; (5) adopt innovative technologies in research and development, such as the use of mineralizers, Carbon capture and utilization, etc.
2. Current status of carbon emission reduction development in the cement industry in North America
There are only two developed countries in North America, the United States and Canada. Their national conditions are basically the same, but they are quite different from Asian countries.
U.S. cement production in 2021 is about 85 million tons, of which Portland cement production is about 83 million tons and masonry cement production is about 2 million tons. The output accounts for about 2% of the world’s total production. The annual carbon dioxide emissions of the cement industry are about 6,400 tons. Ten thousand tons, the carbon dioxide emissions per ton of cement are about 750 kilograms. The development of process technology in the cement industry in the United States is relatively lagging behind. Most of the main equipment of cement plants is imported. Some cement production kiln equipment is old and has low thermal efficiency. The main energy supply fuels are coal and petroleum coke accounting for 60%, and natural gas accounting for about 22%. %, other fuels are biomass fuels, alternative fuels, etc.
The urbanization rate in the United States has reached more than 80%. The cement consumption structure is ready-mixed concrete accounting for 70%~75%, concrete products accounting for 10%, construction accounting for 8%~10%, and others accounting for 8%~12%. The major cement groups in the United States are centered on the cement industry, with well-developed upstream and downstream industrial chains. Most cement groups have their own raw material processing bases and aggregate production bases of a certain scale, cement production plants, rationally arranged concrete mixing stations and cement distribution. At the terminal, all links from the supply of cement production raw materials to the multi-channel sales of finished cement products are guaranteed to a certain extent.
The overall goal of the U.S. cement industry is to achieve carbon neutrality by 2050. The carbon reduction goals in 2030 are an alternative raw material rate of 6.8%, an alternative fuel rate of 20%, an energy efficiency of 3.69GJ/t cement clinker, and a clinker coefficient of 0.85; The carbon reduction goals in 2050 are 10% alternative raw material rate, 50% alternative fuel rate, energy efficiency reaching 2.95GJ/t cement clinker, and clinker coefficient 0.75. To this end, the Portland Cement Association (PCA) in the United States has also proposed a corresponding carbon emission reduction roadmap. The short term is to improve energy efficiency, use recycled waste to replace raw materials, produce low-carbon cement mixing materials, and optimize design to achieve the lowest cost in the life cycle. emissions; in the medium term, increased use of alternative fuels and renewable energy; in the long term, carbon capture and the introduction of new cement-based materials.
Most of the existing cement plants in the United States are relatively old, and the thermal and electrical efficiencies of cement production are low. In recent years, some cement plants have upgraded to precalciner kiln technology and equipment, which has improved energy efficiency, increased the use of industrial waste alternative fuels, and reduced the carbon emission intensity of unit products. The current unit clinker heat consumption is 3.768GJ/t, and the unit cement power consumption is 134kWh/t. The raw material substitution rate for cement production in the United States is 5%, and the fuel substitution rate is not high. The main types are some biomass energy. Since the cement clinker coefficient is greater than 0.9, clinker is the main source of carbon emissions in cement production. The newly developed Portland limestone cement (PLC) allows the addition of 15% limestone in cement, while ordinary Portland cement requires limestone. The addition amount does not exceed 5%. It can be seen that the promotion and application of Portland limestone cement can help reduce carbon dioxide emissions per unit product. In terms of the application of CCUS technology, a cement company plans to build and operate a small commercial chemical plant to convert captured carbon dioxide into low-carbon auxiliary cementitious materials.
Canada’s annual cement production has long been maintained between 12 million tons and 15 million tons. The cement industry emits about 9 million tons of carbon dioxide, and the carbon dioxide emissions per ton of cement are about 670 kilograms. The Canadian cement industry is highly concentrated, with multinational companies such as Holcim Cement accounting for 81% of its production capacity. Canadian cement is exported to the United States, but as U.S. cement consumption declines, exports also fall.
The heat consumption per unit of cement clinker in Canadian cement plants is 3.695GJ, and the electricity consumption per unit of cement is 139kW. The overall carbon reduction goal of the Canadian cement industry is to reduce cumulative carbon dioxide emissions by 15 million tons by 2030, and by 4 million tons annually thereafter, and achieve net-zero emissions by 2050. The Cement Association of Canada (CAC) has proposed a technology roadmap for net-zero emissions in cement production, which also includes improving energy efficiency in cement production, low-carbon cement, alternative fuel technologies, carbon dioxide capture and utilization, and important technological innovations.
Cement manufacturers have begun producing Portland limestone cement (PLC) and mixed cement to reduce the clinker coefficient and reduce carbon emissions by nearly 3 million tons per year. The Canadian cement industry is committed to the use of new alternative fuels, including new biofuels, clean hydrogen and electrification. Carbon dioxide capture and application in the Canadian cement industry is also in the process of being actively promoted. For example, Lehigh Hanson Cement and China Sinoma Energy Conservation Company conducted a feasibility study on a comprehensive carbon capture system that can be obtained from its Edmonton Cement Up to 95% of carbon dioxide is captured in the plant’s flue gas; Lafarge Canada installed a flue gas pretreatment system at the Richmond cement plant to provide technical support for subsequent carbon capture and utilization, while injecting the captured carbon dioxide into cement concrete The technology in the project will be promoted as a pilot project.
3. Current status of carbon emission reduction development in the cement industry in Europe
There are many countries in Europe, but cement production is mostly monopolized by some multinational companies, including Holcim of Switzerland, Heidelberg of Germany, and Old Castle of Ireland. Based on the EU’s unified market mechanism, these cement production enterprise groups are also independently responsible for carbon emission reduction tasks. The European Cement Industry Association (CEMBUREAU) has also formulated a carbon emission reduction roadmap for the cement industry.
The members of the European Cement Industry Association include cement manufacturers from 33 countries, with annual cement production of approximately 240 million tons and carbon dioxide emissions of approximately 150 million tons. The carbon emission reduction roadmap proposed by the association in 2013 aims to reduce carbon dioxide emissions by 2030. Emissions will be reduced by 30% and carbon dioxide emissions will be reduced by 80% in 2050. The European cement industry emits approximately 667 kilograms of carbon dioxide per ton of cement; in order to further reduce carbon emissions, the association proposes the use of decarbonized raw materials, improving thermal efficiency, carbon capture and utilization and other similar methods. The proportion of alternative fuels in the European cement industry is close to 50%, of which biomass fuels account for 16%, and alternative fuels are required to reach more than 90% by 2050, including 50% biomass fuels. Specific carbon reduction technical measures include the following aspects: in the cement production process, obtain and utilize more decarbonized raw materials and alternative fuels through waste sorting and other methods, improve production energy efficiency through technological transformation, and develop new low-carbon Clinker, try to apply hydrogen energy and electrification technology, vigorously promote carbon dioxide capture and application technology, use more mixed materials to reduce the amount of clinker in cement, and adsorb and capture carbon dioxide in the concrete building construction process and the building environment. . It is expected that carbon dioxide emissions per ton of cement will be reduced to 472 kilograms in 2030, and zero carbon emissions from cement production will be achieved by 2060.
Under the framework of the carbon emission reduction route formulated by the European Cement Association, Swiss Holcim Cement has proposed three aspects of carbon emission reduction. Direct carbon dioxide emissions from the application of raw materials and fuels account for about 75% of the total emissions from cement production. Through raw fuel substitution, low-calcium clinker and low-clinker cement production, carbon sequestration in building materials and the built environment, and carbon dioxide capture and utilization, in 2030 Direct carbon dioxide emissions can be reduced to 475 kg/ton ; indirect carbon dioxide emissions generated by electricity consumption account for about 5% of the total emissions of cement production, and indirect carbon dioxide emissions generated by other energy consumption such as logistics account for about 20% of the total emissions of cement production. In 2030 , it can Through technical measures such as the use of new energy in society, indirect carbon dioxide emissions will be reduced to 13 kg/ton and 20%; and by 2050, zero emissions will be achieved in the complete industrial chain of cement production.
In 2020, German Heidelberg Cement’s alternative fuel consumption was 26%, its cement clinker coefficient was 74%, and its carbon dioxide emissions per ton of cement were 576 kilograms. Through the application of alternative fuels and improving energy efficiency, optimizing the kiln system, reducing the cement clinker coefficient, and improving carbon dioxide capture By integrating and applying, promoting circular economy and innovative product development, it is expected that carbon dioxide emissions per ton of cement will be reduced to less than 525 kilograms and 500 kilograms in 2025 and 2050 respectively; through the development and application of new products, new processes and new technologies in the future, cement Production produces zero CO2 emissions.
The carbon reduction technologies proposed by Irish Old Castle Cement include (1) alternative fuel technology: the current alternative fuel rate is 30% on average and the highest has reached 60%; (2) clinker replacement technology: make full use of limestone powder, fly ash, etc. resources to produce type II composite cement with high admixture content; (3) Research, formulate and apply “best available technology” for the cement production process. At present, the heat consumption for burning cement clinker per ton has dropped to 3300MJ. Production power consumption has also significantly decreased.
4. Conclusion
a. Addressing climate change is a common but differentiated responsibility for all countries in the world; the cement industry emits large amounts of carbon dioxide, and reducing carbon emissions is an urgent task facing the development of the industry; currently, some cement production in developing countries is close to carbon peak, In some cases, there is a relatively large increase; in developed countries, cement production capacity and carbon dioxide emissions have been basically locked in, and the task of technological emission reduction is huge.
b. The current carbon dioxide emission reduction technologies in cement production mainly include substitution of raw fuels, improvement of energy efficiency of process equipment, and large-volume application of cement mixing materials; with the development of science and technology, in the future, the utilization of new energy and new process technology and equipment will Research and development, the development of new low-carbon cement and new carbon dioxide capture and utilization technology will surely provide strong technical support for the reengineering of the zero-carbon process of cement production;
c. China is a major cement producer, but its carbon dioxide emissions per unit product are relatively low. With the advancement of the “double carbon” goal and the application of carbon reduction technologies, the cement industry will also usher in major changes in substantial carbon emission reductions. Then achieve green and sustainable development of the cement industry, and make greater contributions to the country’s socio-economic construction and response to climate change.
By Zhongyuan Zhang, Shenjin Fu